Proposed method of mix design is a combination of empirical results and mathematical calculations based on absolute volume method. The water content is assumed to be inclusive of HRWRA content. The procedure is initiated by selecting different mix characteristics or material proportions in the following sequence:
Estimation of yield stress and plastic viscosity
In a mix design procedure, trial batches are prepared in the laboratory and workability is measured after arriving at all the ingredients of concrete. If the workability criterion is satisfied, cubes or cylinders are cast for compressive strength test. If desired level of workability is not obtained, adjustments of the constituents of concrete are again made and trial batch is prepared. The fact that rheological parameters are fundamental properties of fresh concrete and compressive strength is the most important hardened property of concrete, the correlation curves between rheological properties and compressive strength of concrete was used in the mix design. The correlation graphs are presented in Figure 2 and 3. The details of the correlation may be found elsewhere14.
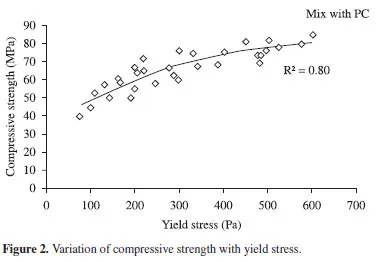
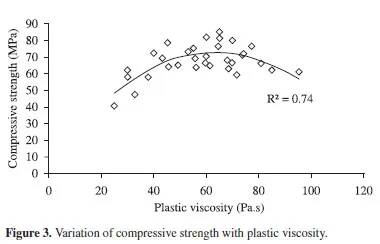
HRWRA dose, sand content
It was observed that optimum dose of high range water reducing admixtures (HRWRA) is around 1.5% by weight of cement beyond which it does not significantly reduce yield stress and plastic viscosity. For yield stress, the optimum sand content is 30% for minimum yield strength; between 30-40% sand, plastic viscosity is minimum. IS code also assumes sand content equal to 28% when zone 2 (medium) sand is used.
Water cement ratio and aggregate-paste volume ratio
Since water-cement ratio is not a good predictor of strength in case of HPC, relationship between water-cement ratio and compressive strength has not been used. In fact, there may be various combinations of water-cement ratio and paste volume to aggregate volume ratio. The water-cement ratio can be obtained from Figure 4 for a given target strength. Extrapolation may be done to obtain values not presented in the figure.
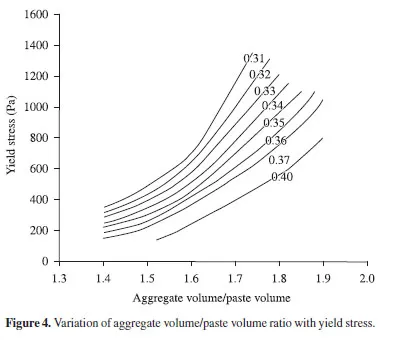
Aggregate content
Coarse aggregate content depends on the particle shape. The coarse aggregate content may be determined from Aitcin1.
Cement content
Cement content may simply be calculated once aggregate volume-paste volume ratio and water-cement ratio is known. Water content here is the free water content including HRWRA.
Correction factors
Corrections are to be made in the mix design for different zones of sand and maximum size of coarse aggregates. To do this, a reference mix as per IS: 10262-1982 has been considered and rheological parameters of this reference mix were obtained with the present rheometer. The reference mix is follows:
- 53 grade OPC = 571 kg/cu.m;
- Indian Standard zone II sand = 436 kg/cu.m;
- Coarse aggregate of nominal size 10 mm = 1083 kg/cu.m;
- Water = 200 L/cu. m inclusive of HRWRA;
- PC as HRWRA = 7.7 kg/cu.m;
- Water-cement ratio = 0.35;
- Percentage sand = 28%.
Now, comparing the values of yield stress and plastic viscosity of the various other mixes with the rheological parameters of the reference mix, correction factors have been calculated and presented in Table 3. These correction factors were derived from the experimental results of the variation of rheological parameters with sand gradation and maximum size of coarse aggregates.
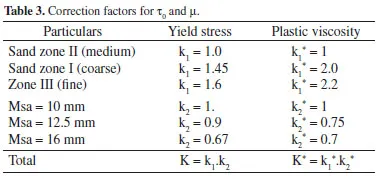
The steps of present mix design procedure are as follows:
- Assume sand = 28% and take air content as follows:
- For 10 mm nominal maximum size of aggregate (Msa): air = 3%
- 12.5 and 16 mm: air = 2.5%
- 20 mm: air = 2%.
These are as per the provisions of IS: 10262-1982.
- Assume HRWRA dose = 1.5% by weight of cement.
- From Figure 2 and Figure 3, read ฯ 0, ยต for target given strength.
- Calculate correction factors: K = k1k2, K* = k1* k2* from Table 3.
- Corresponding to K ฯ0, obtain aggregate volume- paste volume ratio from Figure 4 and choose water-cement ratio.
- Assume quantities of coarse aggregate from Aitcin1, depending on particle shape.
- Calculate cement and water content.