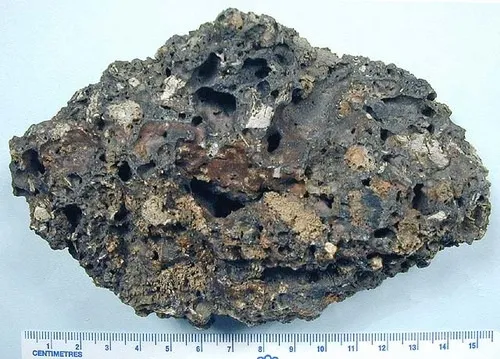
Blast-furnace slag clinker before grinding
Ground, granulated blast-furnace slag (GGBFS) is another industrial by-product sometimes used as a partial replacement for Portland cement. GGBFS is a glassy, granular material produced in blast furnaces as a by-product of the iron and steel-making process. It is another example of a material that used to be considered waste being put to good use.
Compared to concrete made with only Portland cement, concrete that includes GGBFS:
· hardens more slowly;
· produces less heat during hydration;
· continues to gain strength for a longer period of time; and
· produces more durable concrete.
The lower temperatures produced by GGBFS during hydration allow control joints to be placed farther apart. GGBFS is substituted 1-to-1 with Portland cement, and may form up to 70% of the mass of cementicious materials. GGBFS has a specific surface of 1,700 to 2,900 ft2/lb (350 to 600 m2/kg).
Silica Fume
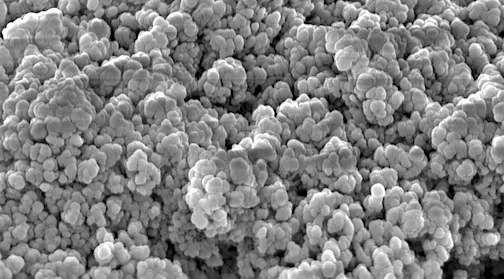
Silica fume magnified 10,000 times
Silica fume is sometimes used to enhance certain properties of concrete. It is a very fine, glass-like powder collected from the flue gases of electric arc furnaces during the process of manufacturing silicon metals. Before the implementation of tougher environmental laws in the mid-1970s, silica fume was not collected. It has now become one of the most valuable and versatile concrete admixtures in the world. Unlike sand – its chemically similar counterpart – particles of silica fume are water-soluble, which means that they can react chemically as part of the hydration process.
When the amounts of two granular materials are equal, materials with smaller particles expose more surface area against which reactions can take place. Silica fume is approximately 100 times smaller than Portland cement particles, and so its small size, along with its relatively high silica content, make it a very highly reactive pozzolan. Their small particle size also allows silica fume to fill in the spaces between grains of cement, called particle-packing, making concrete more dense and less porous or permeable to moisture. It also improves compressive strength, the bonding strength between particulates, aggregates and embedded steel, and improves resistance to abrasion.
Silica fume may form up to 12% of the mass of cementicious materials. Silica fume has a specific surface of 63,000 to 150,000 ft2/lb (13,000 to30,000 m2/kg).
The uniformity of silica fume can vary according to the chemical characteristics of the metal alloys being manufactured. Silica fume from up to four different furnaces is sometimes mixed together in an effort to provide a more uniform product. The effects on concrete of variations in the chemical properties of silica fumes from different furnaces are not well understood. The properties of silica fume concrete also vary with the different properties and amounts of the various water-reducing agents (plasticizers) that are typically used when silica fume is added to concrete. Because the huge surface area of silica fume uses more water and reduces workability, plasticizers and super-plasticizers are added to make concrete more fluid so that it can be placed and worked more easily.
Concrete is typically mixed at local batch plants before being trucked to a job site. Batch plants commonly have silos containing fly ash and often have GGBFS on hand. Permanent storage facilities for silica fume are less common.
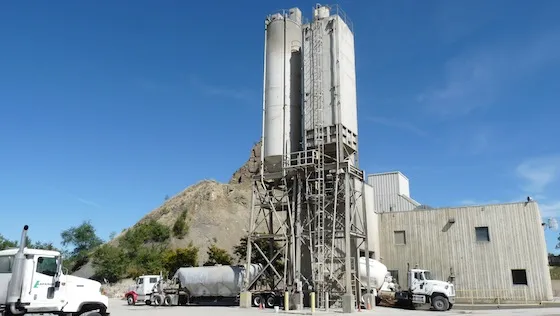
A concrete batch plant with two fly ash silos
AGGREGATES
Aggregates are granular materials that include sand, gravel, crushed stone, river stone, and lightweight manufactured aggregates, and may occupy up to 75% of the concrete’s total volume. Since aggregates are less expensive than cement paste, they are added to concrete to help reduce costs. The properties of aggregates can have a significant effect on the workability of concrete in its plastic state, as well as the durability, strength, density, and thermal properties of the hardened concrete.
Where do aggregates come from?
Aggregates are heavy. Quarrying them in a central region and trucking them long distances is cost-prohibitive, so aggregates are generally quarried locally. This means that the mineral, chemical and physical properties are likely to be different in different areas, depending on the local geology. Minerals with different properties can react differently to chemical processes or conditions in concrete, so aggregates are one more constituent material of concrete that can have properties that vary.
Quarrying Aggregate
Aggregate quarry operations are similar to those used for quarrying stone for cement. The quarry pictured below, also located in Colorado, provides primarily granite aggregate for the asphalt paving and concrete industries.
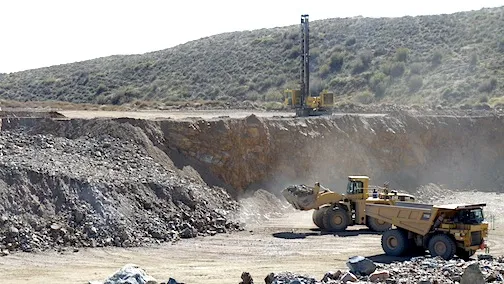
The photo above shows a relatively new quarry being worked. The drilling rig is shown drilling the holes in which explosive charges will be set, while a truck is loaded with stone loosened by previous blasting. The truck will haul the stone to Crusher #1.
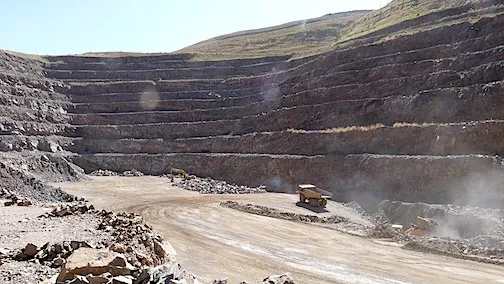
Older quarries have been worked longer, so they are deeper. This operation blasts in holes drilled 35 feet deep, as opposed to 80 feet at the limestone quarry. Here, too, blasting is performed by a subcontractor. This operation contains several quarries in addition to the processing area, so it is a large operation.
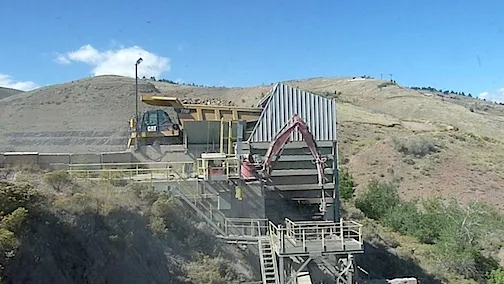
Above, a truck feeds Crusher #1, the first in a series of crushers that the stone passes through. This quarry produces 18 different aggregate products that vary in size from boulders to sand.
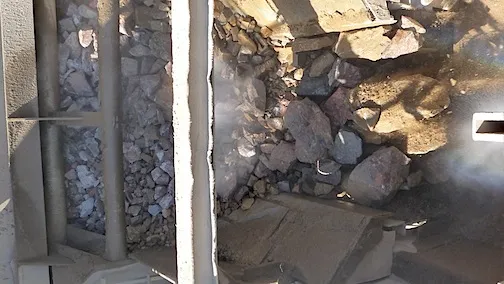
Looking directly down into Crusher #1, the size of the stone before it enters the crusher is visible. The stone is moving from left to right.
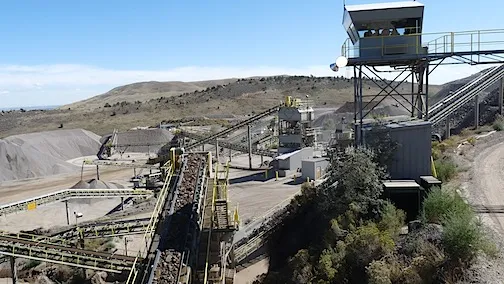
Crushing and sorting operations are monitored from a central control tower overlooking the operations area. The conveyor nearest the camera is moving the stone after processing by Crusher #1.

The photo above shows the view overlooking the operations area, and the controls and monitors.
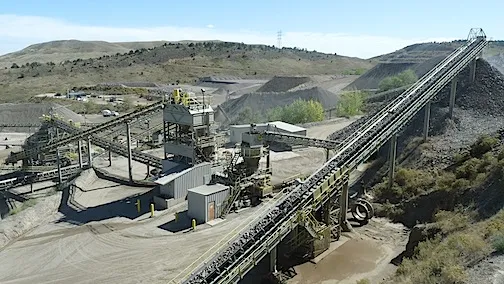
This overview photo shows two additional crushers near the center. Despite massive amounts of stone being crushed, transported, pushed and dropped onto stockpiles, airborne dust was minimal.
Aggregate Size
Aggregates for concrete are generally divided into two categories: fine and coarse. Fine aggregates are generally natural sand or crushed stone, with most particles passing through a 3/8-inch (9.5-mm) sieve. Coarse aggregates generally range between 3/8- to 1-1/2 inches (9.5 mm to 37.5 mm) in diameter. Most coarse aggregate used in concrete is crushed stone, although smooth river rock is also used.
Inadequate amounts of fine aggregates can cause excessive bleeding, difficulties in pumping concrete, and difficulties in achieving smooth troweled surfaces. The bond strength of fine aggregates is not affected much by the shape or texture of the aggregate, since smaller particles offer a large amount of surface area at which bonding to the cement paste can take place. The surface properties of fine aggregate can affect the amount of water required to keep concrete workable. Bear in mind that excessive amounts of water can weaken concrete by increasing the percentage of capillary structure left behind as excess water finds its way to the surface as bleed water and then evaporates. The photos below show aggregates commonly stocked by concrete batch plants.
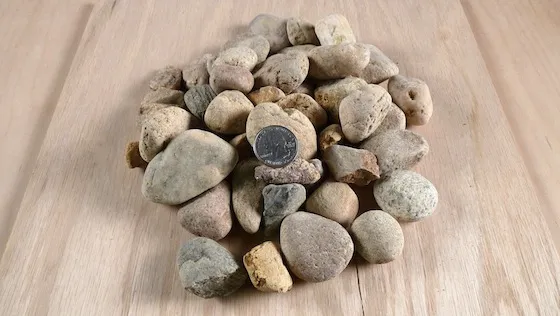
1½-inch gravel
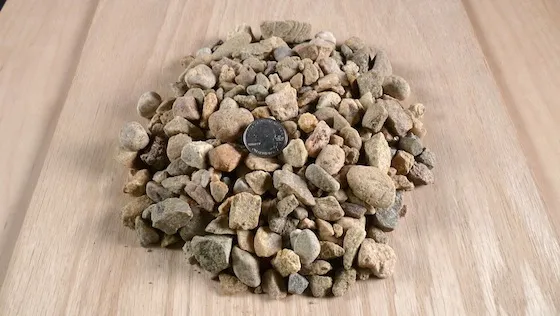
¾-inch gravel
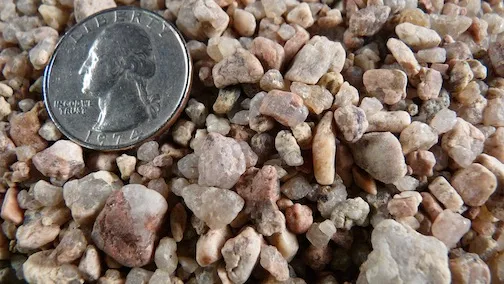
Squeegee
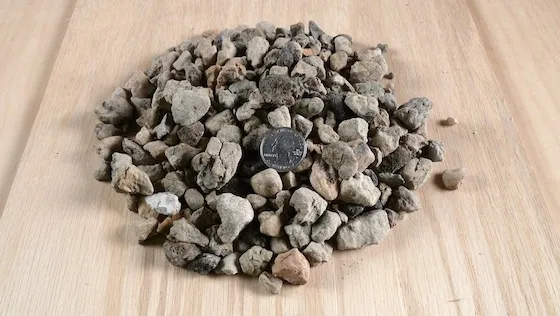
Lightweight
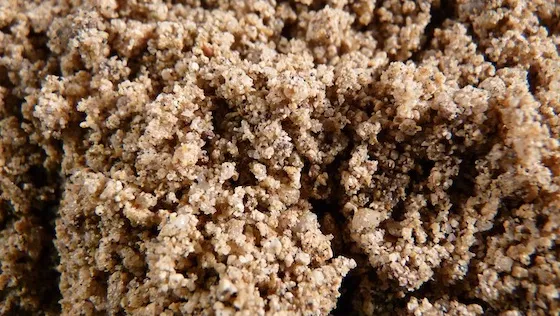
Common sand
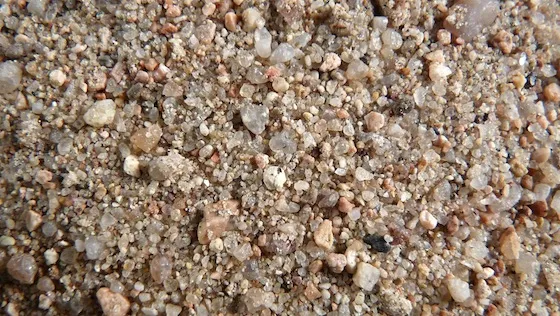
Double-washed sand
The maximum size of aggregate should be less than one-fifth of the narrowest dimension between the sides of forms, one-third the depth of slabs, or three-fourths of the minimum clear spacing between reinforcing bars.
Using the largest possible aggregate size is sometimes recommended to minimize the amount of cement required, as well as to minimize drying shrinkage of the concrete. The disadvantage of using large, coarse aggregate is that it increases the chances of bond failure between the aggregate surface and the surrounding cement paste, since the stresses at the interface between the two materials are higher than with smaller aggregate. It also reduces the total available surface-bonding area.
The rigidity/deformation characteristics of the aggregate are also important. Extreme differences in the properties of aggregate and cement paste result in high stresses that create micro-cracks that can weaken concrete.
Grading Aggregate
Well-graded aggregate is the result of using many sizes of aggregate in the mix. This helps reduce the amount of cement paste required to fill the spaces or voids between the individual aggregate pieces. Reducing the percentage of cement paste in the mix helps reduce shrinkage and lowers the heat of hydration, both of which can crack concrete. It also improves its durability. The amount of aggregate used in a mix is called its packing density. Well-graded aggregate has better packing density than gap-graded aggregate. Gap-graded aggregate has no intermediate-sized pieces, which makes the concrete more difficult to place and increases its cost, and both of these factors can affect the final product.
Moisture Content
Different types of aggregate have different levels of porosity; that is, they can absorb different amounts of water. Highly porous stone affects concrete differently, depending on whether it is water-saturated or dry before being added to the mix. Dry stone will absorb more water from the mix, and this can make concrete stiffer and more difficult to work, which may appear as visible problems in the finished concrete. Water in saturated stone has to be considered when calculating the amount of water to be added to the mix or the water ratio may be too high, resulting in weakened concrete.
There are four moisture levels:
· Oven-dry (OD) means that all moisture has been removed.
· Air-dry (AD) means that surface moisture has been removed and internal pores are partially full.
· Saturated surface-dry (SSD) means that the surface moisture has been removed, and all internal pores are full.
· Wet means that pores are full, and there is a surface film.
Of these four states, saturated surface-dry is considered the best moisture state. With SSD, the aggregate is in a state of equilibrium, so the aggregate will not absorb or give water to the cement paste. However, this moisture state can be difficult to obtain.
Lightweight Aggregates
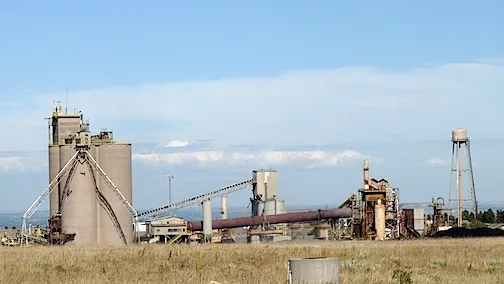
A facility for manufacturing lightweight aggregate
Lightweight aggregates are typically man-made and are highly porous. Clay, shale and slate will expand when they are heated, a little like popcorn. Since most are porous, they are also moisture-absorbent, which can affect the amount of water used in the mix. A few types develop a coating during the fusion process that reduces their absorptive properties; however, if this coating is damaged during handling, the aggregate as a whole will regain some of its ability to absorb water. Depending on the percentage of aggregate that has damaged coating, this condition can affect the quality of the concrete if such a variation is not allowed for in designing the mix.
Heavyweight Aggregates
Heavyweight aggregates are usually used in buildings requiring radiation shielding and are not of concern to most inspectors.
Waste Materials as Aggregate
Many ideas for re-purposing waste materials have been considered and some have been tried. Inspectors may encounter concrete with problems caused by materials inappropriately substituted for aggregate.
Some of those waste materials include:
· building rubble;
· industrial waste; and
· mine tailings.
Alkali-Aggregate Reaction (AAR)
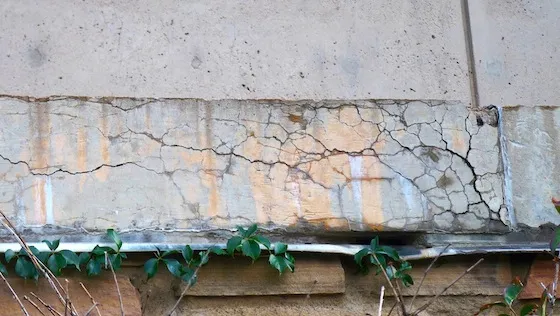
ASR-damaged concrete
Some types of aggregate materials react badly with alkalis from sources in the concrete or from other sources, such as de-icing salts, groundwater, or sea water. If the aggregates contain a large percentage of silica, the reaction is called alkali-silica reaction (ASR). If the aggregate consists of dolomitic carbonate rocks, it is called alkali-carbonate reaction (ACR).
During ASR, which is the more common of the two problems, soluble silica in the aggregate reacts with soluble alkali to produce an alkali-silica gel. When this gel absorbs moisture, it expands, causing concrete to crack. It may take a while after the concrete is placed for ASR to appear. Cracks in control joints, shrinkage cracks, or micro-cracks in the surface that are enlarged by freezing may allow moisture to enter the concrete and be absorbed by the gel. Some aggregates are non-reactive and others are reactive to varying degrees.
There is no cost-effective method for mitigation of concrete damaged by AAR. Correction requires removal and replacement.
Other Aggregate-Related Problems
Some types of stone used for aggregates may cause problems by expanding and contracting during freeze-thaw cycles due to moisture content.
Aggregates can vary in their resistance to wear.
Aggregate impurities consisting of fine, solid particles can interfere with the surface bonding between cement and coarse aggregate.
Aggregate impurities that are soluble may interfere chemically with alkaline cement pastes and affect setting times.
Aggregate from quarries in coastal locations should be cleaned to avoid salt contamination that may affect the concrete chemically or attack embedded steel.
Inspectors will not always be able to attribute problems they see to particular constituent materials. Taking the time to learn about the types of raw materials used in their area and the typical problems that arise related to those materials may help inspectors to better understand the seriousness of various defects they discover so that they can make the appropriate recommendations.
Comments are closed