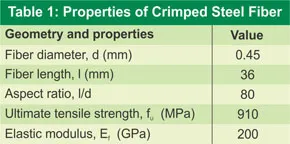
Mechanical properties of fiber reinforcement concrete are needed to use the FRC in various structural applications. This paper presents the experimental investigation carried out to study the behavior of high performance fiber reinforced concrete (HPFRC) under compression and flexure with compressive strength ranging from 60 MPa to 86 MPa and flexural strength ranging from 6 MPa to 10 MPa. Steel fiber volume fraction ranges from zero to1.5 percent (39, 78 and 117.5kg) with aspect ratio of 80 were used. The influence of fiber content on the compressive strength and flexural strength with w/cm ratios ranging from 0.40 to 0.25 is presented. Equations are proposed using regression analysis to predict the strength of HPFRC effecting the fiber addition in terms of fiber reinforcing index. Strength comparison analysis was carried out to validate the empirical equation and the maximum absolute variation obtained was 4 percent. Addition of 1.5 % volume of crimped steel fiber resulted in 10% increase in the compressive strength while flexural strength increased by 37% and the RCSR value evaluated is between 0.107 and 0.149.
Introduction
In last 3 decades, numerous research and development studies have been taken up in the field of steel fiber reinforced concrete (SFRC) for understanding the behavior of sound composites. SFRC has been used in several areas of infrastructure and industrial applications including highway and airport pavements, bridge decks, sky scrappers, hydraulic structures, industrial floors, tunnel lining, etc. [1, 2]. As noted by ACI Committee 544, the composite has great potential for many use in civil Engg., applications, especially in the area of structural elements.
High performance concrete (HPC) is defined according to ACI 363-1992 [3] as concrete, which meets special performance and uniformity requirements that can’t always be achieved by using only the conventional materials and normal mixing, placing and curing practice. Typical high performance requirements specify high strength (above 41 MPa), enhanced impermeability (permeability less than 10-10 m/s), and high tensile strength (above 4 MPa) and other special requirements. HPC is achieved by using super plasticizen (SP) to reduce water/cm ratio and by using SCM (supplementary cementing material) as silica fume having pozzolanic reaction and filler effect, which usually combines high strength with high durability [4].
High-performance/highstrength concrete leads to the design of smaller sections and reduces the dead weight, allowing longer spans and more useful area of structures. Reduction in mass is also important for economical design of seismic resistant structures. is responsible for the enhancement of strength and durability of the concrete [4]. Strength, ductility and durability are the important factors to be considered in the design of earthquake resistant R.C. structures. Due to the inherent brittleness of HPC/ HSC, it lowers its post-peak portion of the stressstrain diagram almost vanishes or descends steeply [5]. This inverse relation between the strength and ductility is a serious drawback for the use of HPC/HSC and a compromise to this drawback can be obtained by the addition of discontinuous short steel fibers in to the concrete. When concrete cracks, the randomly oriented fibers arrest a micro cracking mechanism and limit the crack propagation, thus improving the strength and ductility thereby enhances the durability of structural elements. Wafa and Ashour [6] have reported that addition of steel fibers in to HSC changes its brittle mode of failure in to a more ductile one and results in a small increase in compressive strength and more increase in tensile strengths compared to plain concrete. Fibers with 1 percent volume fraction and aspect ratio of 75 provide maximum stiffness to concrete and results in maximum increase in compressive strength [7]. Although a number of researchers investigated the effect of inclusion of discrete steel fibers on the compressive strength [8, 9, 10], research on HPC where fibers play a major role is lacking. The main objective of this paper is to study the influence of crimped steel fibers on the compressive strength and flexural strength of high performance- fiber reinforced concrete with varying w/cm ratios and 10% silica fumereplacement.
Research Significance
High performance concrete with and without fibers possesses mechanical properties that are significantly different from normal strength concrete materials. This paper presents an extensive experimental investigation on the mechanical properties of HPFRC with w/cm ratios of 0.40, 0.35, 0.30 and 0.25 and studies the effects of inclusion of fiber contents on improving these properties.
Experimental Program
Four basic mixes for plain concrete designated as FC1-0.0, FC2-0.0, FC3-0.0 and FC4-0.0 according to the w/cm ratios of 0.4, 0.35, 0.30 and 0.25 were selected.
Materials and Mixture Proportions
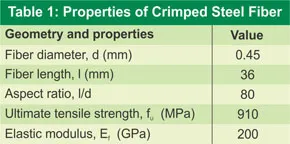
Ordinary portland cement-53 grade satisfying the requirements of IS: 12269–1987 [11] and silica fume supplied by Elkem India Ltd. having specific surface area of 23,000 m2 /kg, a specific gravity of 2.35 and contained 88.7% of SiO2 were used in the ratio of 9:1 (1:1 partial replacement of cement) in all the mixes. Fine aggregate of locally available river sand conforming to IS: 383-1970 [12] with fineness modulus of 2.55 and a specific gravity of 2.63 and coarse aggregate of blue granite crushed aggregates conforming to IS: 383- 1970 with 12.5 mm maximum size and fineness modulus of 6.4, a specific gravity of 2.70 were used.
Fibers used are crimped steel fibers of diameter =0.45 mm and length = 36 mm, giving an aspect ratio of 80. The properties of fibers used are given in Table 1. Mixture proportions used in the test programme are summarized in Table 2 [13, 14, 15]. For each water to cemetitious material ratio three fiborus concrete mixes were prepared with fiber volume fractions, Vf of 0.5, 1.0 and 1.5 percent (39, 78 and 117.5kg/m3). Due to the inclusion of the fibers some minor adjustments in terms different ingredients had to be made as shown in Table 2. A naphthalene sulphonated formaldehyde (NSF) as HRWR admixture (super-plasticizer) conforming to ASTM Type F with dosage range of 1.75% to 2.75% by weight of cementitious materials has been used to obtain the adequate workability of plain and fiber reinforced concrete. Dosage of super plasticizer was arrived based on the workability tests conducted on trial mixes.
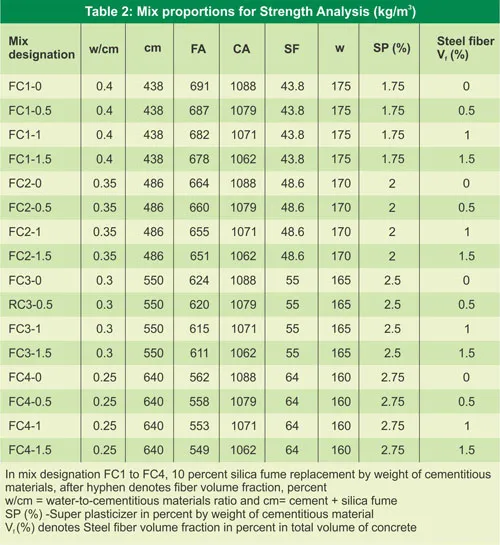
Mixing and Curing
Silica fume was mixed with cement uniformly and thoroughly till homogeneity is attained. Concrete was mixed using a tilting type mixer and specimens were cast using steel moulds, compacted with table vibrator. For each mix at least three 150 mm cubes and three 100 x 100 x 500 mm prisms were produced. Specimens were demolded 24 hours after casting and water cured at 27± 2oC until the age of testing at 28 days. All the specimens were cured in the same water tank to maintain uniform curing.
Results and Discussions
The results of this investigation are applicable to the material and the type of fibers used.
Compressive Strength
Compressive strength tests were carried out according to IS: 516- 1979 [16] standards using 150 mm cubes loaded uniaxially. The tests were done in a servo–controlled compressive testing machine by applying load at the rate of 14 MPa/min. Minimum of three specimens were tested to assess the average strength.
![]() | ![]() |
Figure 1(a) Silica fume concrete cube specimens after failure in compression test | Figure 1(b) Fiber concrete cube specimens after failure in compression test |
Behavior under Compression
Under uniaxial compressive loading, extensive crack was produced in the concrete during pre-peak stage and then failed suddenly at peak load. Figure 1(a) reveals the failure mechanism of Silica fume concrete and indicates that it increases its compressive strength and makes it more brittle, fails violently and suddenly. It is observed from Figure 1(b) that when fibers in discrete form present in the concrete, propagation of crack is restrained which is due to the bonding of fibers in to the concrete and it changes its brittle mode of failure in to a more ductile one and improves the post cracking load and energy absorption capacity.
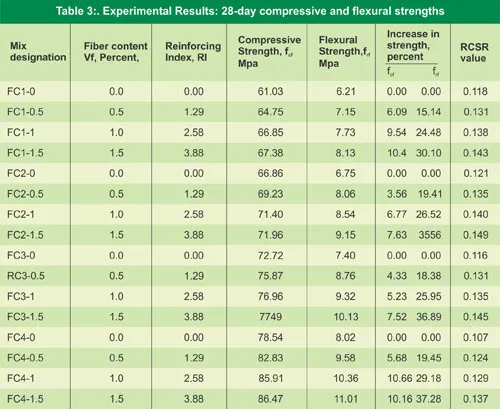
Test results show that addition of fibers has a moderate effect on the improvement of compressive strength values. Table 3 and Figure 2 show that the addition of fiber volume fraction from 0 to 1.5% increases the compressive strength by about 10 percent compared to zero 20 percent given in the literature [5, 7, 9, 10, 17] for normal strength concrete. It is observed from the test results that for 1.0 percent fiber content, the increase in strength is about 10 percent but beyond 1.0% fiber content, there is only marginal increase in strength. Based on the test results, using linear regression analysis, the compressive strength of HPFRC may be estimated in terms of compressive strength of plain concrete, fc and Reinforcing index, RI and volume fraction, Vf respectively, as follows:
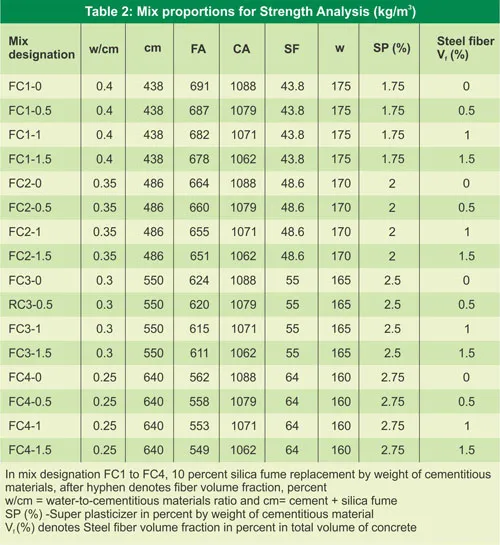
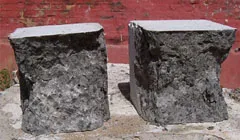
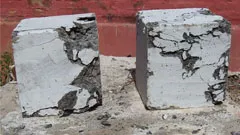
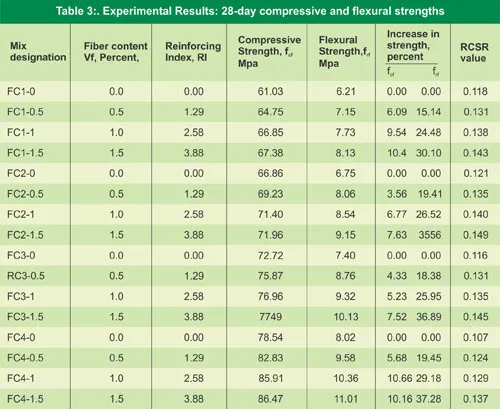
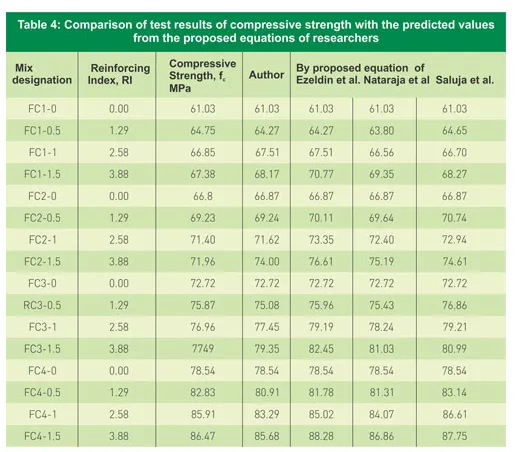
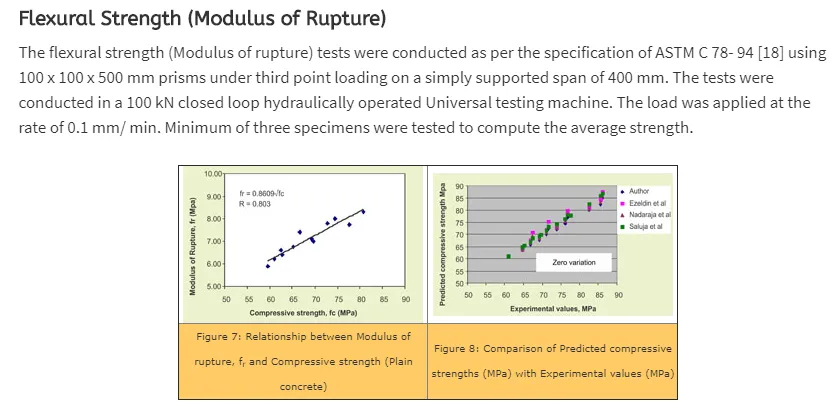
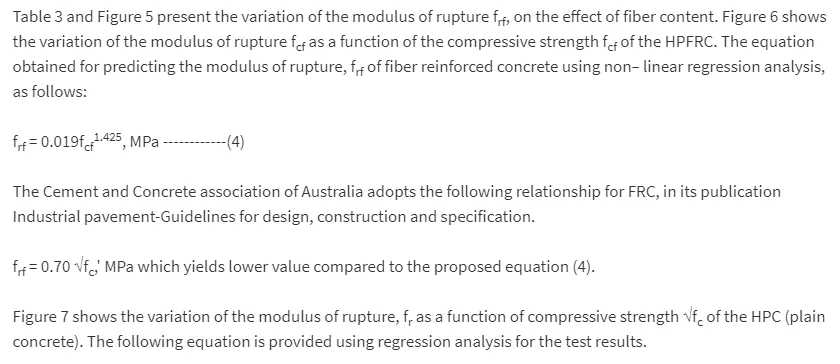
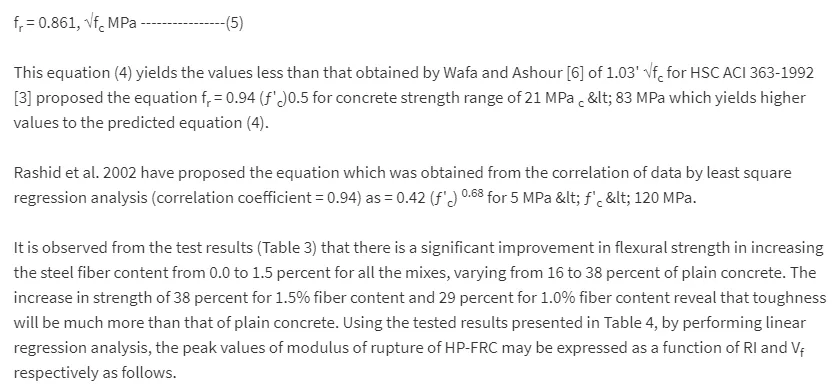
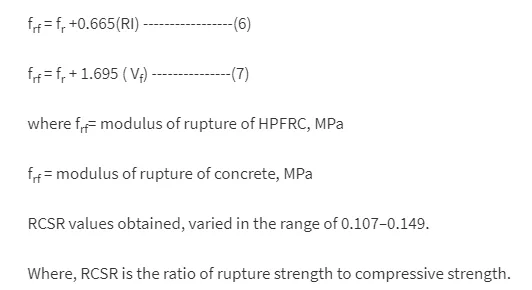
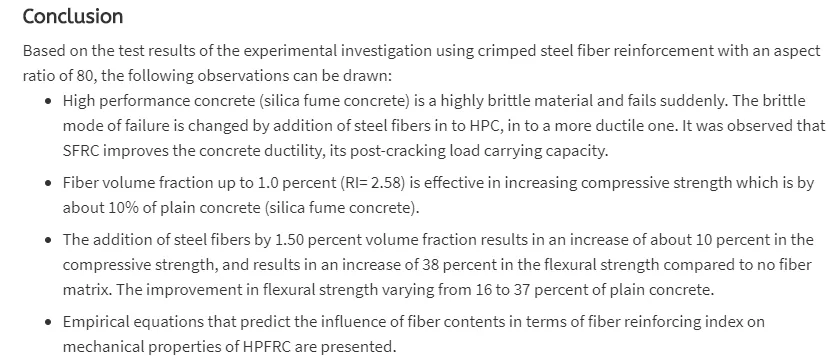

Comments are closed