Prestressed Concrete
Prestressed concrete is a method for overcoming concrete’s natural weakness in tension. Prestressing tendons (generally of high tensile steel cable or rods) are used which produces a compressive stress that offsets the tensile stress that the concrete compression member would otherwise experience due to self–weight and gravity loads. Traditional reinforced concrete is based on the use of steel reinforcement bars, rebar, and inside poured concrete.
Prestressing can be accomplished in two ways: pre-tensioned concrete and bonded or unbounded post-tensioned concrete.
Pre-tensioned Concrete
Pre-tensioned concrete is cast around already tensioned tendons. This method produces a good bond between the tendon and concrete, which both protects the tendon from corrosion and allows for direct transfer of tension. The cured concrete adheres and bonds to the bars and when the tension is released it is transferred to the concrete as compression by static friction.
However, it requires stout anchoring points between which the tendon is to be stretched and the tendons are usually in a straight line. Thus, most pretensioned concrete elements are prefabricated in a factory and must be transported to the construction site, which limits their size. Pre-tensioned elements may be balcony elements, lintels, floor slabs, beams or foundation piles. An innovative bridge construction method using pre-stressing is described in stressed ribbon bridge.
Bonded Post-Tensioned Concrete
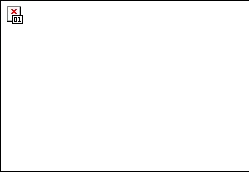
Bonded post-tensioned concrete is the descriptive term for a method of applying compression after pouring concrete and the curing process (in situ). The concrete is cast around a plastic, steel or aluminium curved duct, to follow the area where otherwise tension would occur in the concrete element. A set of tendons are fished through the duct and the concrete is poured.
Once the concrete has hardened, the tendons are tensioned by hydraulic jacks that react against the concrete member itself. When the tendons have stretched sufficiently, according to the design specifications (see Hooke’s law), they are wedged in position and maintain tension after the jacks are removed, transferring pressure to the concrete.
The duct is then grouted to protect the tendons from corrosion. This method is commonly used to create monolithic slabs for house construction in locations where expansive soils (such as adobe clay) create problems for the typical perimeter foundation. All stresses from seasonal expansion and contraction of the underlying soil are taken into the entire tensioned slab, which supports the building without significant flexure.
Post-stressing is also used in the construction of various bridges, both after concrete is cured after support by falsework and by the assembly of prefabricated sections, as in the segmental bridge.The advantages of this system over unbonded post-tensioning are:
- Large reduction in traditional reinforcement requirements as tendons cannot destress in accidents.
- Tendons can easily be ‘weaved’ allowing a more efficient design approach.
- Higher ultimate strength due to bond generated between the strand and concrete.
- No long term issues with maintaining the integrity of the anchor/dead end.
Unbonded Post-Tensioned Concrete
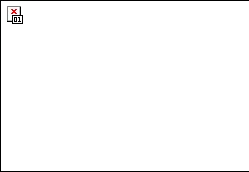
Unbonded post-tensioned concrete differs from bonded post-tensioning by providing each individual cable permanent freedom of movement relative to the concrete. To achieve this, each individual tendon is coated with a grease (generally lithium based) and covered by a plastic sheathing formed in an extrusion process. The transfer of tension to the concrete is achieved by the steel cable acting against steel anchors embedded in the perimeter of the slab.
The main disadvantage over bonded post-tensioning is the fact that a cable can destress itself and burst out of the slab if damaged (such as during repair on the slab). The advantages of this system over bonded post-tensioning are:
- The ability to individually adjust cables based on poor field conditions, e.g., shifting a group of 4 cables around an opening by placing 2 to either side).
- The procedure of post-stress grouting is eliminated.
- The ability to de-stress the tendons before attempting repair work.
Post-Tensioning in Building Structures
Market Factors Favoring the Post-tensioning System
Followings are the market factors, which favor implementing Post-Tensioning system in Building structures:
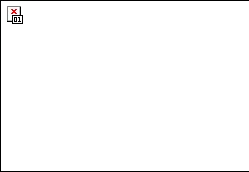
- Longer spans
- Unique designs: irregular shapes
- Shorter construction cycles
- Cost reduction
- Shorter floor-to-floor heights
- Superior structural performance
Direct Cost Reduction
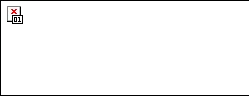
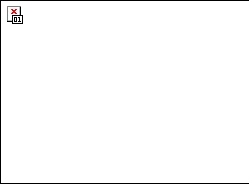
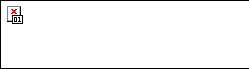
Post-tensioning offers direct cost reduction over conventionally reinforced slabs primarily by reducing concrete and rebar material quantities as well as rebar installation labor. Typically, savings between 10%–20% in direct cost are achieved.
Followings are the factors which contribute to direct cost reduction:
- Less concrete material
- Reduction in slab thickness reduces total building height and cost
- Less rebar
- Less labor cost for installation of material
- Reduced material handling
- Simplified formwork leads to less labor cost
- Rapid reuse of formwork leads to less formwork on jobsite
As a rule, the break even mark between conventional and prestressed solutions is approx. 7m spans.
In a typical slab with spans over 7 meters, the net savings in material cost can range between 10%–20% of original RC alternative. A typical comparative cost structure is shown on the next page:
Material represents 60% of direct cost of a post-tensioning system. Cost structure of PT System is shown there.
Improved Construction Efficiency
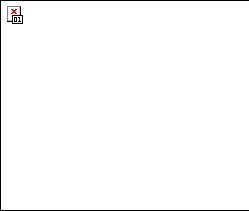
Since post-tensioned slabs are designed to carry their own weight at time of stressing, they can significantly improve construction efficiency and deliver an additional 5%-10% of indirect savings.
Following factors contribute to improved construction efficiency:
- Shorter construction cycles
- Less material handling and impact on other trades
- Simpler slab soffit–less beams and drop caps/panels
- Quicker removal of shoring gives more access to lower slabs
Typical 5-Day Construction Cycle schedule for 800-1,000 m2 of slab is shown below. 3-day cycle is also achievable with early strength concrete and industrial formwork.
Superior Structural Performance
The prestressing in post-tensioned slabs takes optimal advantage of tendon, rebar and concrete properties to deliver an economical structural system.
Factors contributing to superior structural performance are listed here:
- Use of high-strength materials
- Deflection control
- Longer spans are achieved
- Crack control and water-tightness
- Reduced floor-to-floor height
- Lighter structure requires lighter lateral load resisting system
- Economy in column and footing design
- Reduced noise transmission compared to RC
- Lower total cost of ownership (maintenance) compared to RC alternatives
Typical Quantities
Post-Tensioning and rebar rates vary greatly depending on span configuration and loading. Compared to other countries, PT projects in US are designed with less loading and lower PT and rebar rates.
Bonded System
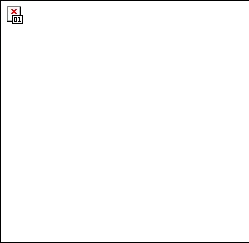
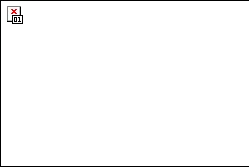
US values (1 kN/m2 SDL & 2.5 kN/m2LL)
- 3 – 4 kg/m2 of PT
- 5 kg/m2 of Rebar
With higher loading (3 kN/m2SDL & 3 kN/m2LL)
- 3.5 – 5 kg/m2of PT
- 7 – 9 kg/m2of Rebar
Unbonded System
US values (1 kN/m2SDL & 2.5 kN/m2LL)
- 3.75 kg/m2of PT
- 6 kg/m2of Rebar
Project Parameters
- Gross Floor Area–Superstructure: 72,000 m2
- Typical Floor Gross Area: 11,000 m2
- Total Floors: 7
- Typical Floor Slab Spans: 10 m max / 8 m avg.
Type and Location
- Type of Structure: High-end Residential
- Location: Dubai, UAE
- Construction Date: Aug 2004 – Jan 2005
Project Team
- Prime Structural Engineers: Adnan Saffarini
- Contractor: SBG
- Client: Private Investment
- PT Supplier: Freyssinet Gulf
- PT Value Engineers: ADAPT Corporation
Design Criteria
- Design Code: BS-8110
- Concrete Compressive Strength Fcu: 40 MPa
- Reinforcement Yield stress:460MPa
- Superimposed Dead Load: 6 kN/m2
- Design Live Load: 2 kN/m2
Original Design
- Original Floor System: Hourdy Slab System
- Depth of Floor System: 380 mm
- Boundary Beams: Yes
Alternative Design offered by Freyssinet & ADAPT
- Post-tensioned Floor System: 2-way Flat Plate
- Depth of Slab:220 mm
- Boundary Beams: None
Benefits
- 70 % less rebar
- 13 % less concrete
- Elimination of all Hourdy Blocks
- Unified structural slab system
- Beams & drop caps were deleted, simplifying slab installation
- 25% less formwork
- 3 months shorter construction program
- 15% savings in site overhead and plant
Comments are closed.