Concrete is a composite material consisting of a binder, which is typically cement, rough and fine aggregates, which are usually stone and sand, and water. These comprise the constituent materials of concrete. But because of the many variables of the raw materials and how they are processed and combined, there are many opportunities for problems to appear in concrete. Having a fundamental understanding of the different materials and manufacturing processes may help those who inspect concrete to know what problems to look for, where to look for them, and how to recognize them.
In simple terms:
· cement + water = cement paste;
· cement paste + sand = mortar; and
· mortar + stone = concrete.
Admixtures may be included in the mix to control setting properties.
The chemical reactions that take place when different constituent materials are combined can vary depending on the properties of the individual materials. The materials can vary in their chemical makeup and performance characteristics, depending on where they were mined or quarried, and according to the manufacturing methods used and conditions in the manufacturing plant.
Binders
Binders are fine, granular materials that form a paste when water is added to them. This paste hardens and encapsulates aggregates and reinforcement steel. Immediately after water is added, cement paste begins to harden through a chemical process called hydration. Hydration takes place at different rates according to the different properties of the binders and admixtures used, the water-to-cement ratio, and the environmental conditions under which the concrete is placed. The ways in which binders affect concrete, mortar and similar products can vary with the chemical and physical properties of the source materials, the constituent materials, the mix design, and, to a lesser extent, the variations in the cement manufacturing process.
Portland Cement
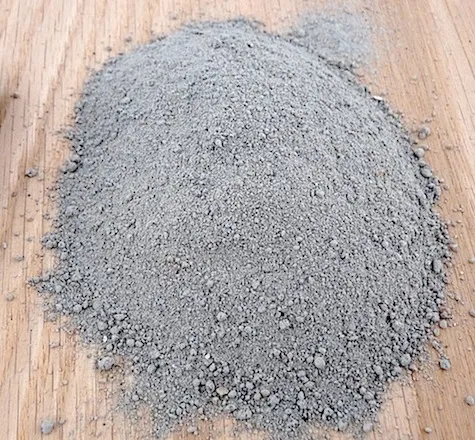
Portland cement
There are different types of cement, but Portland cement is the binder used most widely. Although Portland cement is named after an area in England where its use was originated, today it is manufactured all over the world.
ASTM International defines Portland cement as “hydraulic cement (cement that forms a water-resistant product) produced by pulverizing clinkers consisting essentially of hydraulic calcium silicates, usually containing one or more of the forms of calcium sulfate as an inter-ground addition.”
Portland cement is made by fusing calcium-bearing materials with aluminum-bearing materials. The calcium may come from limestone, shells, chalk, or marl, which is a soft stone, or hard mud, sometimes called mudstone, that is rich in lime.
The Cement Manufacturing Process
The basic operations of cement plants are roughly similar but may vary according to location. The manufacturing process that follows describes what takes place in a quarry and cement plant in Colorado.
Quarry Operations
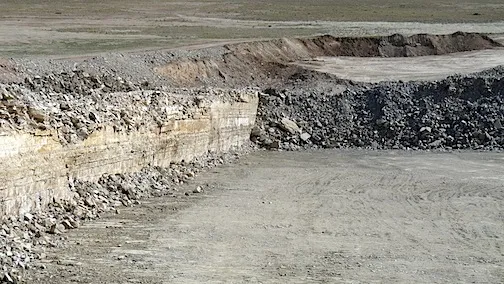
A limestone layer about 18 feet thick breaks the surface and slants away underground. Quarrying operations follow it down to a level of about 200 feet before it is no longer profitable to pursue.
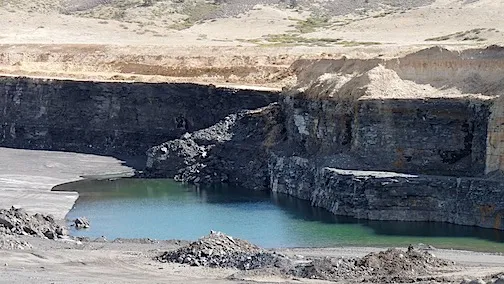
The dark-colored rock pictured above contains limestone and two kinds of shale, all of which are used in producing cement. The light-colored material is called over-burden, which is not used in manufacturing, but is set aside to be replaced later during reclamation after the quarry has reached the end of its permit period and is closed.
The flat area in the quarry wall, called the lift or bench, is the depth to which holes are drilled before charges are set for blasting. Here, it is about 80 feet. Because of Homeland Security requirements, most quarries subcontract the blasting operations.
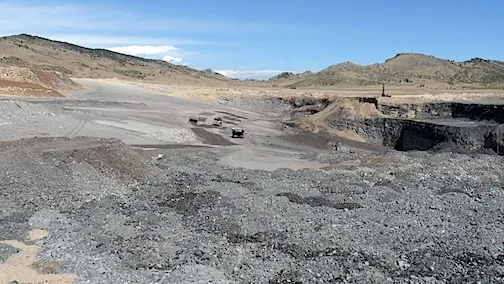
After blasting, the waste stone is brought to the end of the quarry where quarrying first began. It will be the first material to be filled back in as part of the reclamation process. Usable stone is hauled by truck and either dumped into the primary crusher or piled nearby.
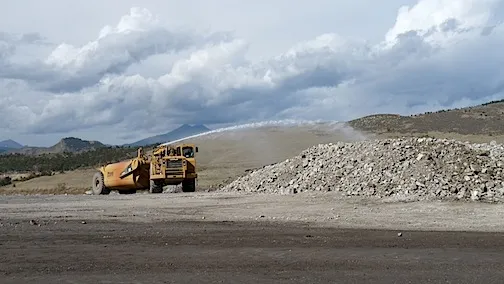
The roads and piles must be kept watered to reduce airborne dust.
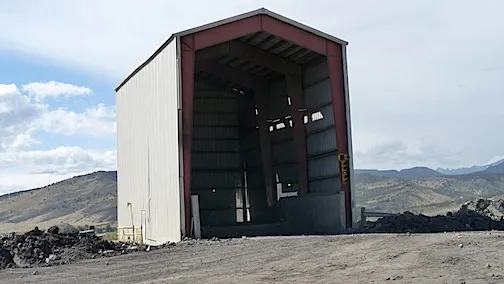
Trucks back into this building to dump their loads into the primary crusher.
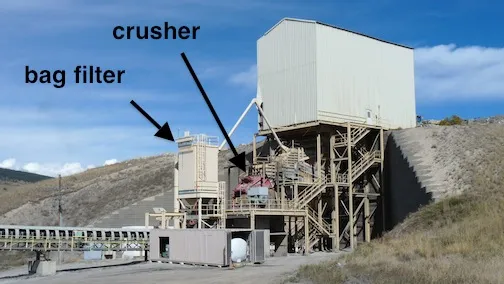
The primary crusher
After the stone is dumped into the feed chute from above, gravity moves it down through the crusher, which reduces it to about 3 inches in diameter. A bag filter helps reduce airborne dust.
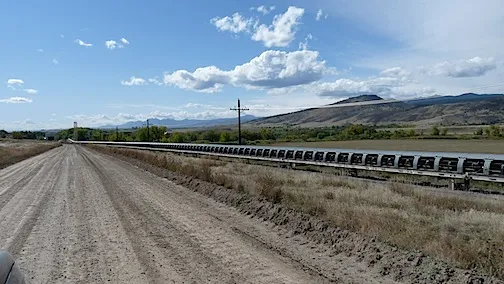
From the crusher, the stone moves onto a conveyor belt that carries it to the manufacturing plant about 2 miles away.
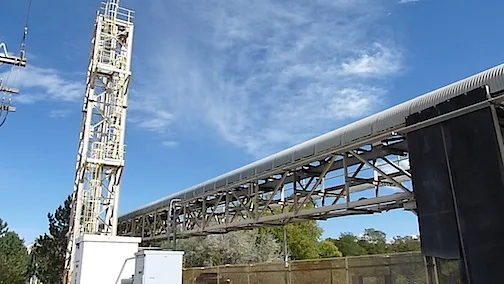
Long conveyor belts must be kept adjusted to the proper tension. This is done by using steel cables to suspend concrete weights inside the towers.
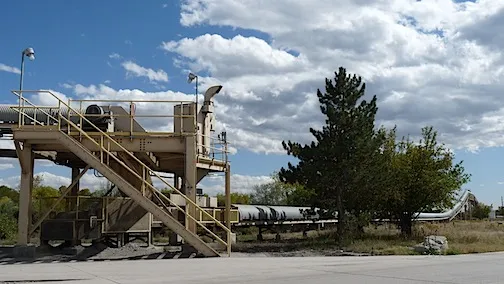
At each point where the conveyor changes height or direction, another bag filter helps to remove dust from the crushed stone and from the air.
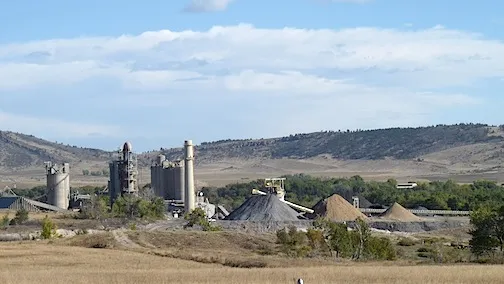
The limestone and shale are finally stockpiled at the far end of the production line.
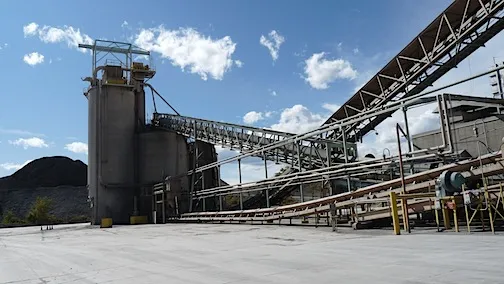
The stone is loaded with a front-end loader one bucketful at a time onto a conveyor that carries it into the surge silo (above left). From the surge silo, the stone can be conveyed into the system at a uniform rate. From the surge silo, the stone is transported to a dryer that removes most of the moisture before returning it to the secondary crusher (center silo), where it is reduced to about 3/8-inch in diameter. From this point, the stone is transported by high-speed air instead of by roller-supported belts.
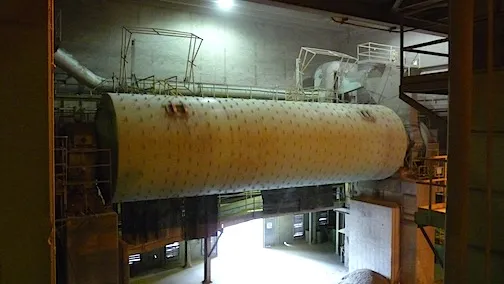
The dried, crushed stone is then moved to the ball mill, in which tumbling steel balls reduce it to a powder. The ball mill is a spinning cylinder that has a sacrificial lining held in place by hundreds of bolts, the heads of which can be seen in the photo above.
Different materials are combined in the ball mill, so this is also where initial blending takes place. Common materials are limestone, shale, sandstone and iron.
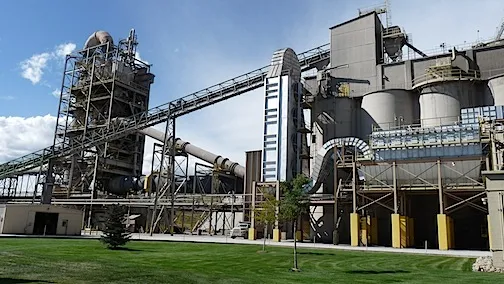
From the ball mill, the material moves to the pre-heat tower (at left), where it is heated to about 1,800° F before moving to the horizontal, cylindrical, rotating kiln.
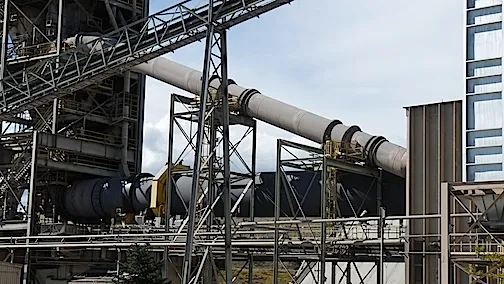
The kiln (dark grey) is tilted slightly so that the material moves through it as it rotates. The more steeply inclined tube above the kiln (light grey) supplies combustion air, as does the U-shaped duct at the top of the pre-heat tower. Inside the kiln, the material is heated to about 3,300° F. This process is called sintering. Chemical changes take place that result in the formation of a marble-sized substance called clinker. Creating clinker means using heat to drive all carbon dioxide out of the material. Carbon dioxide is a major greenhouse gas.
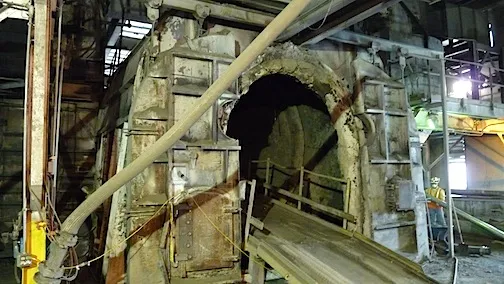
The photo above shows the doors open at the lower end of the kiln, which is shut down for inspection and service. The 6-inch-diameter flexible pipe slanting down to the left is the gas supply for the burner that ignites the pulverized coal fuel. The end of the 8-inch coal supply pipe can be seen just to the right of the feet of the worker.
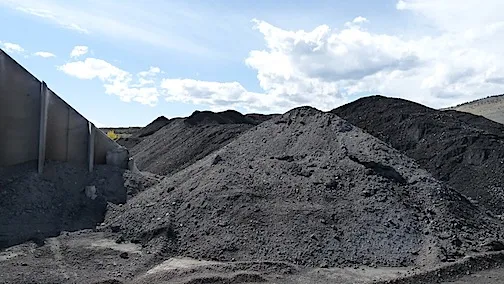
Stockpiles of the pulverized coal used to fuel the kiln
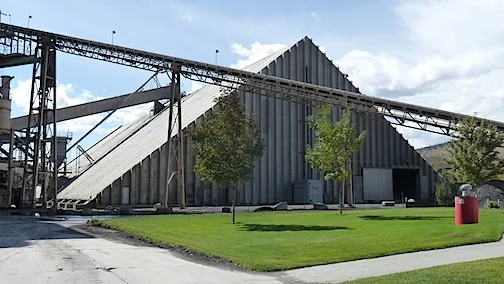
Clinker is moved to a specially-shaped storage shed to control its moisture content.
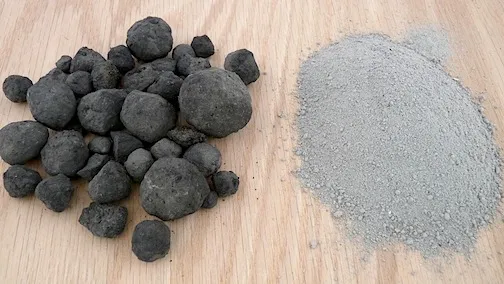
Clinker is finely ground to create the final cement product. The photo above shows both the marble-sized clinker before being ground, and the final product: cement.
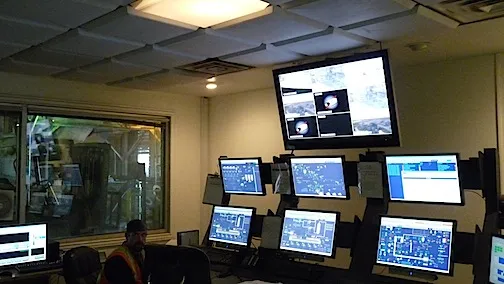
The entire operation is monitored and controlled from a central control console that contains numerous monitors with real-time digital readouts.
Variations
Although there are ASTM standards with which Portland cement may comply, there are a number of factors that can cause its performance characteristics to vary.
Particle Size
The size of the particles is important because particles that are ground more finely offer more surface area against which the chemical reactions take place, and these strongly influence the properties of the cement. Cement with small particles will be more reactive and will gain strength sooner after the hydration process has begun. The total surface area of the particles in a given volume of material is called its specific surface.
Portland cements have a specific surface of 1,500 to 2,000 square feet per pound of material (ft2/lb), equal to around 300 to 400 square meters per kilogram (m2/kg), depending on type.
Gypsum and Sulfates
Gypsum, also in the form of ground particles, is mixed with the ground clinker to slow the hydration process enough so that there will be time to place the concrete, screed it, and finish it before it sets. If gypsum or sulfate materials are added to and ground with the clinker material, they may be reduced in size more quickly than the clinker. This preferential grinding can result in smaller particles, which increases their ratio of reactivity compared to that of the clinker material.
For any particular cement, there is an optimum content for both gypsum and sulfate. The details of exactly how sulfates affect the strength development of concrete are not well understood.
The optimum content of both gypsum and sulfates depends not only on the type of cement design mix, but also on the:
· chemical properties of both the calcium and aluminum source materials used for the clinker;
· physical properties of the aluminates, such as crystal size;
· varying solubility of the different sources of the sulfates;
· particle size;
· milling temperature; and
· use of admixtures.
As if this weren’t complicated enough, the optimum sulfate content for one cement property, such as strength, may be different from the optimum content for another property, such as drying shrinkage. Concrete and mortar can have different optimum contents, which is why different types of cements are manufactured.
Materials are tested four times during the manufacturing process in an effort to prevent such problems. The raw materials are tested before they enter the manufacturing process, before entering the kiln, after leaving the kiln, and before final storage in the main storage silos.
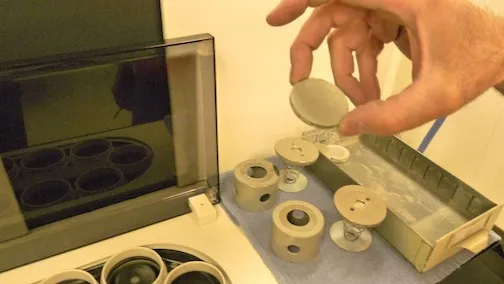
Cement wafers used in a portion of the testing process
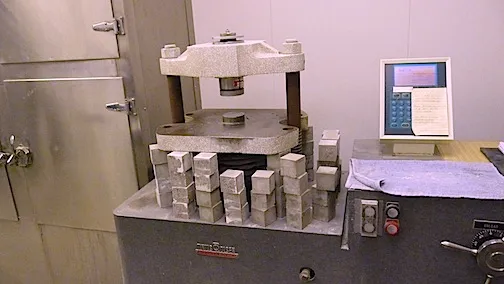
Equipment used to test compressive strength
Comments are closed.