Methods of corrosion protection, corrosion inhibitors, corrosion resistant Steels, coatings and cathodes protection
Corrosion is defined as the process of deterioration (or destruction) and consequent loss of a solid metallic material, through an unwanted (or unintentional) chemical or electro-chemical attack by its environment, starting at its surface, is called Corrosion. Thus corrosion is a process of ‘reverse of extraction of metals’.
Corrosion Mechanism – Wet or Electro-Chemical Corrosion
Corrosion of steel concrete is an electro-chemical process. When there is a difference in electrical potential, along the reinforcement in concrete, an electro-chemical cell is set up. In the steel, one part becomes anode (an electrode with a +ve charge) and other part becomes cathode, (an electrode with a -ve charge) connected by electrolyte in the form of pore water, in the hardened cement paste. The +vely charged ferrous ions Fe+ at the anode pass into solution, while the -vely charged free electrons -pass through the steel into cathode, where they are absorbed by the constitutents of the electrolyte, and combine with water and oxygen to form hydroxyl ions (OH). These travel through the electrolyte and combine with the ferrous ions to form ferric hydroxide, which is converted by further oxidation to rust.
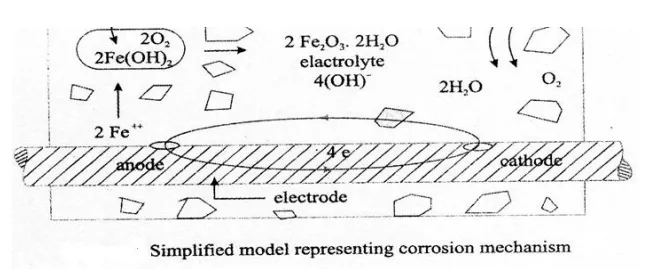
The reactions are described below:
Anodic Reactions:
Fe – – > Fe+++ 2e–
Fe+++ 2(OH)2 – – > Fe(OH)2
Fe(OH)2.2H2O +O2 — > 4Fe(OH)3
Cathodic Reaction
4e– +O2+H2O — – > 4(OH)
It can be noted that no corrosion takes place if the concrete is dry probably below relative humidity of 60%, because enough water is not there to promote corrosion. it can also be noted that corrosion does not take place, id concrete is fully immersed in water, because diffusion of oxygen does not take place into the concrete. probably the optimum relative humidity for corrosion is 70-80%
The products of corrosion occupy a volume as much as 6 times the original volume of steel, depending upon the oxidation state. Figure below shows the increase in volume of steel, depending upon the oxidation state.
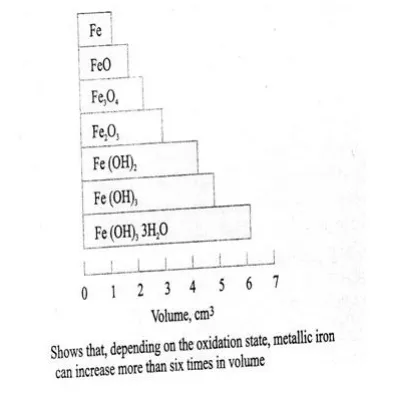
It may be pointed out that though the 2 reactions Fe2 and OH originate iron the anode and cathode respectively, their combination occurs more commonly at the cathode, because the Sn. aller Fe2+ ions diffuse more rapidly than the larger OH ions. So, corrosion occurs at the anode, but rust is deposited at or near the cathode.
Increase the oxygen content has 2 effects :
(i) it forces the cathodic reaction to the right, producing more OH- ions and
(ii) it removes more electrons and therefore, accelerates the corrosion at the anode.
Each of these effects, in turn, supply more reactants for the forming reaction. Obviously, presence of oxygen greatly accelerates both corrosion and rust formation, with the corrosion occurring the entire anode, but the rust forming at the cathode.
Corrosion Inhibitors
A corrosion inhibitor is an admixture that is used in concrete to prevent the metal, embedded in concrete form cording. There exists various types of inhibitors like Cathode, Anode, mixed and Dangerous, Safe.
Of the available corrosion inhibiting materials, the most wide used admixture is based on calcium nitric. It is added to the concrete during mixing of concrete. The typical dosage id of the order of 10-30 litres per m3 of concrete, depending on the chloride levels in concrete.
In the high pH of concrete the steel is protected by a passivating layer of ferric oxide, on the surface of steel. (passivation may be defined as ‘phenon enon in which a metal or an alloy
exhibits a much higher corrosion resistance, than expected from its positon in the electrochemical series.
Passivity is the result of the formation of a highly protective, but very thin, (about 0.0004mm thick) and quite invisible film on the surface of metal or an alloy, which makes it more fine). However, the passivating layer also contains some ferrous oxide, which can initiate corrosion, when the chloride ions reach the steel. The nitrite ions present in the corrosion inhibiting admixture will oxidize the ferrous oxide
Passivating layer even in the presence of chlorides. The concentration of nitrite must be sufficient, to cope up with the continuing ingress (entrance) of chloride ion.
Calcium nitrite corrosion inhibitor comes in a liquid form, containing about 30% calcium nitrite solids by weight. The more corrosion inhibitor is added, the longer the onset of corrosion will be delayed.
Since most structures in a chloride environment reach a leyel of about 7 Kg of chloride iron per m3 during their service life, use of less than 18 litres/m3 of calcium nitrite solution is not recommended.
Figure shows that without an inhibitor, the reinforcing steel starts to corrode, when the chloride content at the rebar reaches a threshold level of 0.7Kg/m3. Although the corrosion process starts when the thereshold level is reacted, it may take several years for staining, cracking & spalling to become apparent, (clear) and several more years before deterioration occurs.
Adding calcium nitrite increases this corrosion thereshold. When you ass 20 litres/m3, corrosion will not begin until over 7.7 Kg/m3 of chloride is present in the concrete at the rebar.
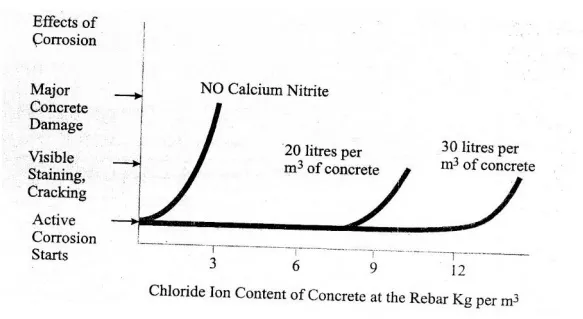
Cathode Protection
Cathode protection is one of the effective, well known, and extensively used methods for prevention of corrosion in concrete structures in more advanced countries. Due to high cost and long term monitoring required for this method, it is not very much used in India.
The cathode protection comprises of application of impressed current, to an electrode laid on the concrete, above steel reinforcement. This electrode serves as anode and the steel reinforcement, which is connected to the negative terminal of a DC source acts as a cathode.
In this process, the external anode is subjected to corrode and the cathode reinforcement is protected against corrosion and hence the name ‘Cathode Protection’.
In this process, the -ve chloride ions, which are responsible for the damage of the passivating film, are drawn away from the vicinity of steel towards the anode, where they are oxidized to form chlorine gas.
The other recent development in corrosion control methods are Re-alkalization and De-salnation. The re-alkalisation process allows to make the concrete alskline again and passivate the reinforcement steel, by electro-chemical method. This brings back the lost alkalinity of concrete of sufficiently high level to reform and maintain the passive layer on the steel.
In the desalination process, the chloride ions are removed form the concrete, particularly from the vicinity of the steel reinforcement by certain electrical method to re-establish the passive layer of the steel.
It appears that the application of cathodic systems for protection of concrete structures, offers some real hope to the concrete technologist, but the field remains open for the introduction of innovative methods to overcome problems of both technique and cost.
Corrosion Resistant Steel
It is found that susceptibility of mild steel to corrosion is not significantly affected by composition, grade or level of stress. Hence substitute steel for corrosion resistance must have a significantly different composition. Based on some success in atmospheric corrosion, weathering steels of the corten type were tested in concrete.
They did not perform will in moist concrete, containing chlorides. It is observed that weathering corrode in similar concrete environments, to those causing corrosion of high-yield steel. They noted that although the total amount of corrosion was less, than would occur on high-yield steel under similar conditions, deep localized pitting developed, which could be more structurally weakening.
Stainless steel reinforcement has been used in special applications, especially as fitments in precast members, but is generally too expensive to use as a substitute for mild steel. Very high corrosion resistance was shown by austenitic stainless steel in all the environments, in which they were tested, but the observations of some very minor printing in the presence of chlorides lead to the warning that crevice corrosion susceptibility was not evaluated in the test program.
High titanium alloy bar is being used in some countries. This bar is grouted into holes, drilled into the marble stabs, and the grouts are based either on Portland cement or Epoxy.
4 Coatings for Steel
The object of coating to steel bar is to provide a durable barrier to aggressive materials, such as chlorides. The coatings should be robust to withstand fabrication of ribcage, and pouring of concrete and compaction by vibrating needle.
Simple cement slurry coating is a cheap method for temporary protection, against rusting of reinforcement in storage.
Central electro chemical Research institute (CECRI), Karaikudi, have suggested a method for prevention of corrosion in steel reinforcement in concrete. The steps involved in this process are
· Derusting
The reinforcement are cleaned with a derusting solution. This is followed without delay by leaning the rods, with wet waste cloth and cleaning powder. The rods are then rinsed in running water and air dried.
· Phosphating
o Phosphate jelly is applied to the bars, with fine brush.
o The jelly is left for 45-60 minutes, and then removed by wet cloth an inhibitor solution is then brushed over the phosphated surface.
· Cement Coating
Slurry is made by mixing the inhibitor solution, with Portland cement and applied on the bar. A sealing solution is brushed after the rods are air cured. The sealing solution has an insite curing effect. The second coat of slurry is then applied and the bars are air dried.
· Sealing
Two coats of sealing solution are applied to the bars, in order to seal the micro-pors of the cement coated an to make it impermeable to corrosive sails.
The is patent method evolved by CECRI, and licence is given to certain agencies. Somehow or other, this method has not become very popular. Some experienced consultants and engineers doubt the effectiveness of this method.
It is one of the effective methods of coating rebars. The fusion bonded epoxy coating is a specialized job, carried out in a factory, and not at site of work. Plants are designed to coat the straight bars in a continuous process. Initially, the bar is shot blested to remove all mill scale and to give the kind of surface finish required.
This ensures an adequate bond between epoxy and steel. The bar is then heated to a carefully controlled temperature, before passing thorugh a spray booth. Eletrostatesically charged epoxy powder particulars are deposited evenly on the surface of the bar. It looks greenish in color, the coating thickness vary from 130 to 00 microns.
Although epoxy coated bars have an excellent protection to corrosion in aggressive environment, there are a few limitations.
After the treatment, cutting and bending may injure the steel, which needs certain sit treatment. The site treatment is likely to be inefficient. The presence of any defect in the treated body can induce severe localized corrosion, which defeated very purpose. The bars cannot be welded. The epoxy is not resistant to rays of sun.
The bars should not be exposed to sun for long duration before use. The coating may get damage during vibration of concrete. The treatment is very costly, as that of steel. This method of protection to the steel is being given to all the flyovers, and other structures at Mumbai.
Galvanized Reinforcement
Galvanizing of reinforcement consists of dipping the steel bars in molten zinc. This results in a coating of zinc, bonded to the surface of steel. The zinc surface with calcium hydroxide in the concrete, to form a passive layer and prevents corrosion.
Comments are closed